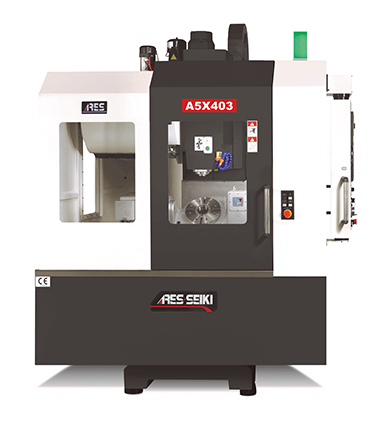
5 Axis CNC Tapping Center
feature
- Spindle speedSTD. 10000rpm
OPT. 12000rpm
15000rpm
20000rpm
24000rpm - Spindle motorMitsubishi 5.5/3.7 kw
Fanuc 5.5/3.7 kw
Siemens 4.8 kw - Rapid traverse X,Y,Z: 48/48/48 m/min
- X axes travel 400mm
- Y axes travel 500mm
- Z axes travel 400mm
- Tools capacity 20+1 tools
- ATC time (T-T) 2.2sec
- Table size Ø255 mm
PRODUCTS
introduction
Advatages of ARES MACHINERY's 5 Axis CNC Tapping Center
By reducing the need for manual adjustments, a CNC drill tap machine contributes to an overall improvement in the accuracy of the manufactured part.
The utilization of 5 Axis CNC Tapping Center yields several cost-saving benefits. Improved tool life reduces the frequency of tool replacements. Enhanced accuracy minimizes the risk of costly mistakes or material wastage. Additionally, these machines reduce the floor space requirements, increase flexibility and spindle usage, decrease the need for expensive fixtures, and lower the overall inventory investment.
The utilization of 5 Axis CNC Tapping Center enables the handling of intricate shapes and designs with ease. This includes various components such as those found in hydraulic systems, water pump housing, gear box housing, gear wheels, injection molds, oil and gas equipment, medical devices, and blood transfusion equipment, among others.
A 5-axis CNC tapping machine allows the cutting tool to not only approach the workpiece more closely but also be positioned at a 90° angle to the surface of the part. This enables optimal cutting conditions at all times. Furthermore, the presence of the fourth and fifth rotational axes allows for the use of shorter cutting tools, resulting in reduced vibrations and an enhanced surface finish. The primary objective of these additional axes is to enable the cutting tool to precisely access all five sides of the part.
Specifically designed to efficiently and swiftly remove even the most challenging materials, a 4+1 or full five axis machining centers significantly reduces the need for manual effort. This leads to heightened efficiency and stability during the machining process.
By incorporating a 5 Axis CNC Tapping Center into your operations, part manufacturers and contract manufacturers can significantly enhance the flexibility of their production processes. This advanced machine tool offers a wide range of applications, enabling you to optimize your machinery for both large-scale and small-scale manufacturing orders. Unlike lower-cost standard machines with limited capabilities, 5-axis CNC machines provide the necessary versatility to meet diverse production requirements.
Moreover, these machines are particularly well-suited for the current manufacturing landscape, characterized by a higher mix of products and lower volumes. In such an environment, where mass production is less prevalent, the ability to deliver machined parts in smaller batches and repeat them as needed becomes crucial.
ARES MACHINERY would like to give you best solution in your machining with your tapping, welcome to contact us right now.
specifications
Unit | A5X403 | ||
---|---|---|---|
Table size | mm | Ø255 | |
Max. Table load | kgf | 50 | |
Max. Workpiece dimennsion (Ø × height) | mm | Ø360 × 250 | |
Min. indexing precision of C axis rotary | degree | 0.001 | |
Cumulative indexing precision of C axis | sec | 15 | |
C axis repeatability accuracy | sec | 4 | |
Slope angle of A axis | degree | ±110 | |
Cumulative indexing precision of A axis | sec | 60 | |
A axis repeatability accuracy | sec | 8 | |
Max. Speeds for A, C axis | rpm | 16.6/25 | |
X, Y, Z axis travel | mm | 400 × 500 × 400 | |
3 axes rapid traverse | m/min | 48 / 48 / 48 | |
3 axes bidirectional accuracy of positioning | mm | VDI 3441 | |
3 axes bidirectional repeatability of positioning | mm | VDI 3441 | |
Spindle speeds | rpm | 10000 | |
Spindle taper | BT30 | ||
Pull stud | MAS 403 P30T-1(45° ) | ||
Spindle driving | Direct-drive | ||
Spindle nose to table | mm | 30 ~ 430 | |
Spindle center to Z path | mm | 570 | |
Spindle motor | Mitsubishi | kw | 5.5 / 3.7 |
Fanuc | kw | 5.5 / 3.7 | |
Siemens | kw | 4.8 | |
X drive motor | Mitsubishi | kw | 1.5 |
Fanuc | kw | 1.6 | |
Siemens | kw | 2.3 | |
Y drive motor | Mitsubishi | kw | 1.5 |
Fanuc | kw | 1.6 | |
Siemens | kw | 2.3 | |
Z drive motor | Mitsubishi | kw | 3.0 |
Fanuc | kw | 3.0 | |
Siemens | kw | 3.3 | |
A drive motor | Mitsubishi | kw | 1.5 |
Fanuc | kw | 1.6 | |
Siemens | kw | 2.3 | |
C drive motor | Mitsubishi | kw | 1.0 |
Fanuc | kw | 1.0 | |
Siemens | kw | 2.3 | |
Tools capacity | tools | 20+1 | |
Max. tool weight | kg | 4 | |
Max. tool length | mm | 200 | |
Max. tool diameter (alternate pocket empty) | mm | 60 (80) | |
ATC time (T-T) | sec | 2.2 | |
Tool Change type | Arm type | ||
Tank volume | L | 260 | |
Coolant pump rate | W | 600 × 2 pcs | |
Flow rate | L/min | 136 | |
Chip flush type | Flushing type | ||
Auto. Chip conveyor | OP | ||
Net weight | kg | 3900 | |
Floor space | mm | 1970 × 3032 × 2700 |
- Tool change time supplied with Mitsubishi controller and standard 60Hz power. For electrical requirements other than this standard, please contact one of our personnel.
- The company reserves the right to modify the specifications / design, subject to change without further notice.
Actual specifications, based on order content.